Equipment
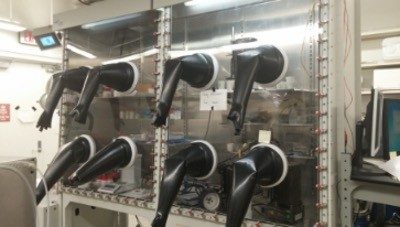
Dr. Zhang’s laboratory is currently equipped with five Inert Corporation glove box systems. The larger custom glove box has eight gloves and an internal working dimension of 96”×65”×31”. The other three glove box systems (PureLab HE 2500 and PureLab HE 1950) with 4 glove ports have an internal working dimension of 77”×35”×31” and 98”×35”×31”, respectively. The glove box systems are composed of antechambers, safety glass window, oval glove ports, vacuum pump, gas management system, integrated oxygen and moisture analyzers (0-1000ppm). By purging with argon gas, an inert environment can be maintained inside the glove box with an oxygen and moisture concentrations as low as 1 ppm. The oxygen and moisture concentration can be monitored and controlled within the glovebox vis a touchscreen interface. Antechambers on the side of the gloveboxes allow material to be brought in or out of the glovebox while keeping the desired environment within the glovebox. Within the glove box are shelves for material storage, electrical power strips and ports for cables/leads connected to equipment outside the glove box like potentiostat.
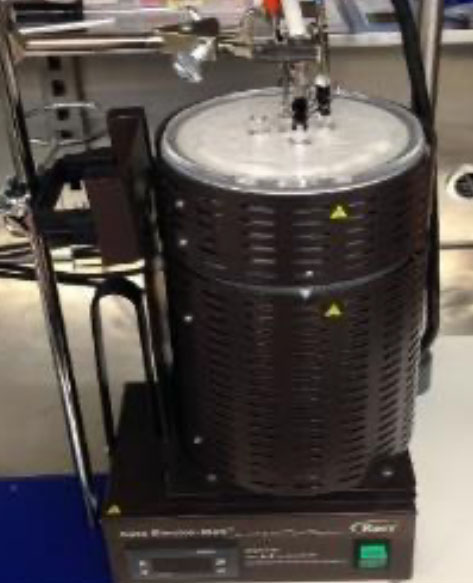
Dr. Zhang’s lab is equipped with 7 high-temperature furnaces (Kerr Auto-Electromelt). These electronic furnaces are placed inside the glove box system to melt the salts and metals for molten salt and liquid metal corrosion tests. The furnace holds the salt or metal temperature within ±3°C of set-point up to a maximum of 1120°C.
The high temperature electrochemical cell is composed of a furnace, crucible, custom lid and electrodes The furnace is used to heat the molten salt inside the crucible to a desired temperature. Crucible made of various materials including nickel, stainless steel and glass carbon are available. Custom lid is made for each furnace to insert the electrodes for conducting electrochemical measurement. The top ends of the three electrodes (working, counter and reference electrode) are connected to the potentiostat outside the glove box via leads.
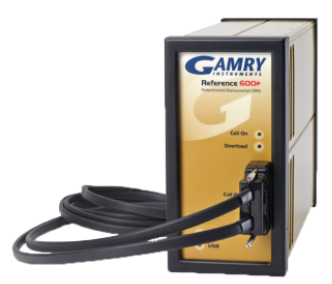
Dr. Zhang’s lab is equipped with five potentiostats (nine Gamry Interface 1000 and one Gamry Reference 600+). Both models are research-grade potentiaostat/galvanostat/zero resistance ammeter which are capable of performing all electrochemical measurements including physical electrochemistry (e.g., cyclic voltammetry, chronoamperometry, etc), pulse voltammetry, DC corrosion (e.g., potentiodynamic polarization), electrochemical nosie, electrochemical impedance spectroscopy, etc. The signal of current can be detected as low as 60 pA (10-12A) with a resolution of 20 aA (10-18A) for Reference 600+ while Interference 1000 only goes down to 10 nA with a resolution of 3.3 fA (10-15A). Compare to Interface 1000, Reference 600+ has a higher performance for fast, low-current measurements. The electrochemical measurement can be performed by the potentiostat and Gamry Framework software. The results can be analyzed by the packaged software Echem Analyst.
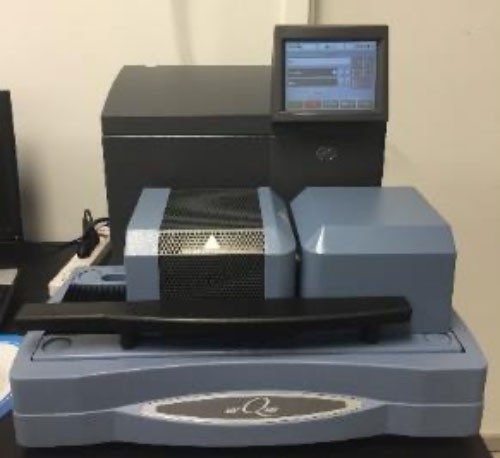
This instrument can provide data such as enthalpy and phase transition temperature leading to phase diagram determination. The phase transition temperatures are determined by measuring the heat input necessary for a sample to match the temperature of a reference sample as the instrument’s furnace changes temperature. This instrument has operation capabilities from room temperature up to 1500˚C with a balance sensitivity of 0.1 g. In addition, hermetically sealed crucibles can be used to ensure air reactive samples retain purity in an inert environment from sample preparation to the completion of testing.
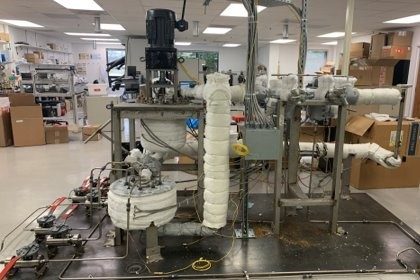
A high temperature forced circulation molten salt loop is available at Virginia Tech to study the effects of flow induced corrosion on materials in molten salts. The system has two functions: 1) to perform the flow Induced corrosion tests and 2) to conduct the electrochemical tests. The molten loop is designed for a high temperature application with design ratings of 730°C temperature and 25 to 30 gpm (at 10 ft. head) flow rate. Due to the low vapor pressure of the molten salt, the system will always be pressurized below 15 psi during operation. Loop components are still designed for a higher-pressure rating of 100 psi, to accommodate the pressure required when the salt solution is transferred from the storage tank to the auxiliary tank and vice-versa for draining and maintenance purposes.
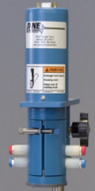
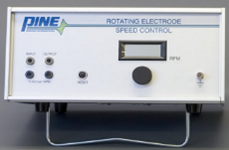
Five modulated speed rotators manufactured by Pine Research Instrumentation. The MSR consists of a motor, rotation speed control unit and electrical connection port to potentiostat. The cylinder electrode made of the studied material can be assembled in the motor and rotated at a controlled speed. The adjustable rotating speed ranges from 50 to 10,000 RPM with an accuracy within 1% of the reading display. The rotating electrode has a well-known flow dynamic characteristic and has been widely used for the electrochemical study at flowing condition. Such system can be used to simulate fluid flow. (molten salt, liquid metal, water)
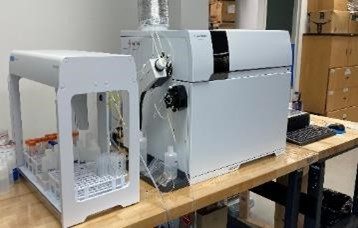
The Agilent 7800 ICP-MS system provides exceptional performance, capable of trace-elemental analysis in high matrix environments with octuplet reaction system cell technology that effectively removes polyatomic interferences. Its unique high matrix introduction technology reduces sample preparation and reduces signal suppression as it can accurately analyze samples that contain up to 3% dissolved solids without dilution. The system incorporates method development software for various applications, allowing for the ability to produce reliable results with tuning and auto-optimization. The integrated measurement system allows smooth transition between different cell modes, simplifying complex system setups to reduce data acquisition times. Coupled with the sample introduction system and autosampler, together, they provide a synergy to maximize throughput and productivity, with the ability to conduct 360 sample measurements in a single run.
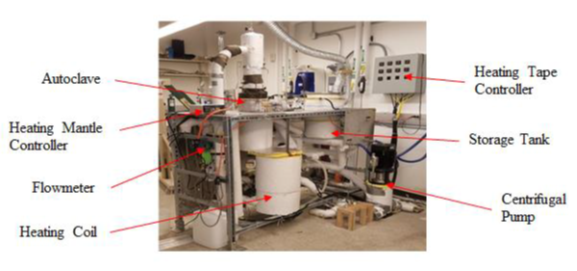
The loop is combined by two sub-loops with one is a pre-heating loop and the other one is the main testing loop. It is designed to study the corrosion kinetic in-line by water (high or low temperature) with water chemistry control, the maximal temperature is 150 oC and pressure is 120 psi. Solution samples for ICP analysis can be taken at the inlet and outlet of the test section simultaneously. The loop is made of stainless steel SS316L.
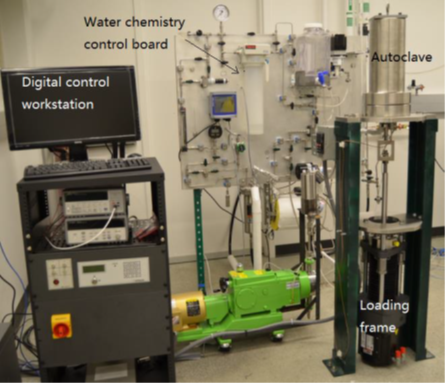
The loop is designed to on-line monitor SCC growth rates. The operation temperature and pressure are up to 360 oC and 2200 PSI. The crack growth rate will be measured by high accuracy DCPD method with an active constant K load control. The loop has a chemistry control unit to simulate PWR and BWR water chemistry. The loop is made of stainless steel SS316L.
The laboratory is equipped a Model5K Servo Creep controller, which is designed as a general-purpose instrument, therefore, the uses are limitless: from creeping testing to fatigue analysis. The 5K Servo is capable of controlling tensile loads continuously up to 5000 lbs or temporarily up to 7500 lbs, over the full 3.25 inch stroke capacity of the frame. The 75-inch per minute actuator rate will quickly and accurately maintain the desired control point. The control panel can be manually or remotely configured to control the load, stroke or strain control point in real-time. A built-in waveform generator can be programmed to cycle or ramp the control point for hours, days or even months for unattended testing. Since the 5K Servo contains a closed loop digital PID controller, the control point is accurately managed in real time. The system is integrated with an autoclave system and a DC potential drop crack monitoring hardware (DCPD), which make the system more powder to test the mechanical properties of a steel in high-temperature and different environments, and on-line measure the crack growth.
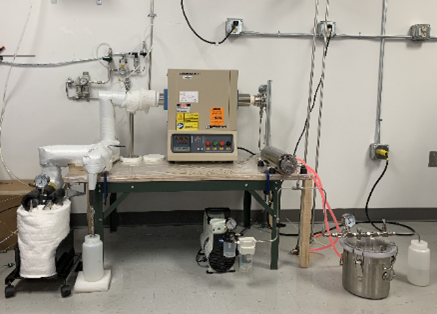
This facility has the capability of conducting continuous steam tests at temperatures up to 1400°C and a flow rate of 200ml/min. The behavior of the material under transient steam environments can also be simulated using a ramping process built-into the system. Steam corrosion experiments will be conducted in a tube furnace in conjunction with a steam generator, as shown in the figure. Deionized water would be transferred into the steam generator periodically after all gases are evacuated inside the steam generator reservoir using a vacuum pump, achieving a max vacuum pressure up to 29.8 mmHg. The data acquisition system will continuously log the instantaneous temperature of the steam environment and flow rate of water into the steam generator.

Low-Temperature Glasscell utilizes a three-electrode electrochemical system to investigate the corrosion behavior of materials in low-temperature and different flow environments. A rotating cylinder electrode with a speed-controlled rotator (0 rpm to 6000 rpm) will be used as the working electrode. Various modifications of working electrode design are adapted to simulate laminar and high shear flow conditions. Solution temperature can be maintained within ±1 °C up with operating temperatures up to 85°C. The test solution can be exposed in the atmosphere via a condenser, which is used to avoid the test solution's evaporation. The in-situ changes of thickness and porosity of the film at different flow rates can be monitored by the electrochemical impedance spectrometry measurements, which can also provide useful information about the electrode reaction's kinetics. Potentiodynamic polarization curves can be used to obtain the corrosion rate, and also investigate the kinetics of the occurring anodic and cathodic reactions on the material surface at different flow rates.
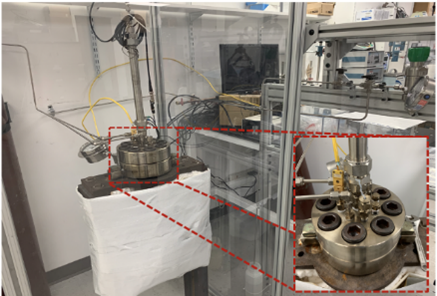
This water corrosion SS316 autoclave is designed to accommodate corrosion and electrochemical measurements in aqueous environments up to 400°C and 15 MPa. The system includes three electrodes (working electrode, counter electrode, and reference electrode) for electrochemical measurement which includes electrochemical impedance spectrometry (EIS) for the study of oxide layers, and potentiodynamic polarization to determine the corrosion behavior of materials. The autoclave also has an in-situ pH monitor, temperature controller, and pressure controller. All electrodes and sensors are designed and fabricated to work under high temperature and high pressure. The inner oxidized coating layer of autoclave allows the investigation of various aqueous chemical environment.
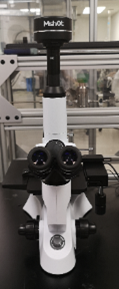
The IM-3000 inverted metallurgical microscope is a bright-field microscope coupled with infinite plan achromatic objective lenses from 4x up to 100x magnification. It is combined with a 16 Megapixel Digital camera to record high-resolution photos and videos.
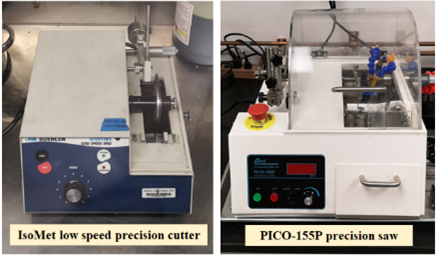
There are two slow cutters available, one is IsoMet low speed precision cutter (0-300 rpm) that is used to deal with radioactive materials, and the other one is PICO-155P precision saw (50-1500 rpm) for the non-radioactive materials. Both cutters can section the materials (such as HT9, stainless steel, etc.) with extreme accuracy (capable of cutting to a ±0.01in [ ±0.25 mm] precision).
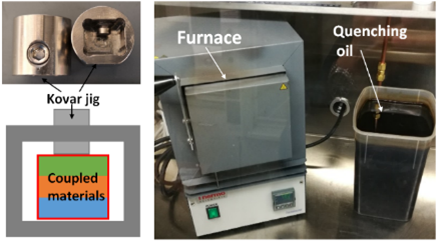
Diffusion couple tests are a common method to investigate the interactions between fuel (uranium alloy) and cladding (such as Fe or HT9). The diffusion couple tests are performed by coupling the materials together with a Kovar jig and then annealing in a furnace for a period of time. To minimize the oxygen effect, the jig is sealed in a Ti crucible, and the furnace is placed inside a glovebox. To maintain the high temperature equilibrium phases, the samples will be quenched after annealing. The interface interactions are characterized by various methods such as SEM/EDS, TEM, XRD, etc.
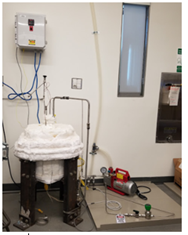
The molten salt autoclave system is used for purifying the chloride and fluoride salt-mixtures and to conduct short to long duration static corrosion tests for different kinds of alloys. The system consists of a 316 SS autoclave chamber which holds the crucible containing the salt and the alloys. The system is designed with capabilities to operate up to 900 ºC temperature and 160 psig (11 bar) pressure. Firstly, the salt-mixture is thermally purified under continuous argon gas flow by adopting a slow and sequential heating schedule, while also ensuring the temperatures do not exceed the hydrolysis temperature of pure compounds. Once the metallic and non-metallic contaminants are reduced, the salt is then used to conduct static corrosion tests for at least 100 hours. The effectiveness of the purification process is checked by analyzing the salt using XPS, XRD and ICP-MS, while the corrosion behavior in alloys is studied through the morphological examination of the corroded specimens using SEM-EDS.
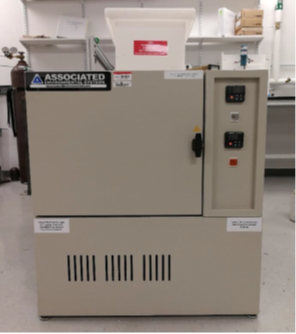
Multiple samples can be tested simultaneously. The system can perform stability tests for extended periods and cycling tests with various soak times at multiple temperatures and humidity set points. The system can be applied to understand the corrosion in a spent fuel dry storage canister.
The laboratory also has oxygen and moisture sensor to be used measure and control the oxygen and moisture level in the experimental environments
The high pressure and temperature aqueous reference are used for various corrosion measurements such as polarization, galvanic corrosion, electrochemical impedance spectroscopy (EIS), and corrosion potential measurements. This electrode provides a stable reference potential when it is used in normal water chemistry, high radiation environments, hydrogen water chemistry, or in aqueous environments with any chemical additions, where the potentials are referenced to standard hydrogen electrode. The electrode has been designed for continuous operation at 290ºC for over 2 years before replacement is needed. Besides, the electrode can operate at pressures above 2,000 psig and it is able to withstand rapid depressurization events as well as thermal ramps of up to 485ºC/min.
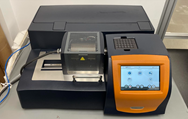
TA Instruments SDT650 is capable of measuring phase transition, specific heat capacity, and vapor pressure. The instrument can perform both differential scanning calorimetry (DSC) and thermogravimetric analysis (TGA) simultaneously. The temperature range is from ambient to 1500°C. In DSC analysis, the heat flow is measured as a function of temperature and time. This can be used for phase transition determination and specific heat capacity measurement. The phase transition can be determined from the peak on the heat flow curve. The specific heat capacity can be measured either using the three-run method (ASTM Standard E1269) or modulated DSC method (ASTM Standard E2716). In TGA analysis, the amount and rate of change in sample mass is measured as a function of temperature and time. This can be used for vapor pressure measurement.
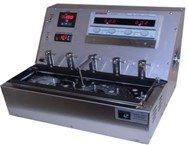
The E399 CC electro polisher polishes alloys by electrolytic removal with a PVDF coated electrolyte bath size of 18” x 6” x 6,” which comes which a temperature controller for varying polishing temperatures. The unit is capable of constant current to 50A or voltage polishing to 30V. The polishing time can also be controlled based on the varying sample areas and desired amount of surface material removal. The electrolytic removal by means of electrical potential and current allows an anodic film to form on the surface of the removal of material ion by ion. This results in a microscopically smooth and virtually featureless material surface without inducing stresses on the surface.
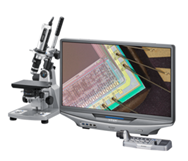
The VHX-970 digital microscope comes with a free angle stand with 90-degree tilt and a rotating stage, capable of mapping 3D topography composition with 2 phase 1-micron motor resolution. The system is coupled with a magnification lens of 20-200x range with 1-inch working distance and compatible with multiple lenses. Topography measurements from the system is NIST traceable, where images are displayed on a 4K monitor. This microscope is suitable for grain size measurements and fracture surface analysis with accurate resolutions down to the micron range.
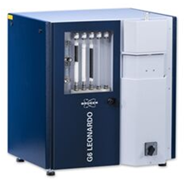
G6 Leonardo comes with a dual element OH analyzer where trace amounts of oxygen and the lowest hydrogen concentrations in the ng/g (ppb) range reliably, without compromises. Each of the elements is measured using a smart molecule sequence where smart analysis is set up, and exact temperature control results in less dust, offering system stability, and higher uptime. Samples enter into a graphite crucible and are melted in the furnace with a fusion control system. The fusion control system comprises an external pyrometer for direct temperature reading and temperature control up to 3000°. Monitoring the temperature allows for better control of when the elements are released and allow for better repeatability in sample measurements. During the measurement process, oxygen from the sample melt will react with graphite crucible to form CO, and carrier gas is used to pass CO and H2 through nondispersive infrared detectors, where the sequence directly measures the concentration of oxygen with 1:1 of CO to O, and thermal conductivity detector is used to measure the concentration of H2. The optimization of the method allows fast analysis times with available results ready in minutes.
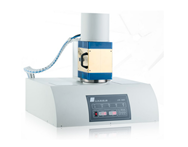
It is a benchtop equipment to determine Thermal Diffusivity, Conductivity and Specific Heat. The samples are subjected to a high intensity radiant energy pulse for a short time. The absorbed energy by sample is emitted on the top of the sample and causes a temperature increase which is detected by Infrared Detector. The system can be used to measure the thermal diffusivity, thermal conductivity and heat capacity.
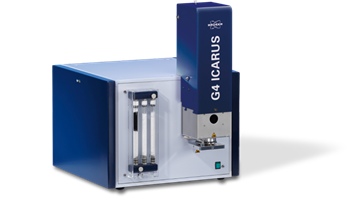
Combustion analyzer with high-frequency induction furnace equipped with rapid detection for carbon and sulfur analysis with detection limits down to 0.4ppm. Carbon and sulfur concentration measurements by CO₂ and SO₂ through combustion. Carbon measurements by a non-dispersive infrared detector and sulfur detection through UV-absorption provide a stable linear dynamic range not affected by temperature variations.